When it comes to choosing the right capping machine for your production line, the decision between 4-wheel cappers and rotary cappers can significantly impact your efficiency and output. Understanding which option aligns with your production scale is crucial.
4-wheel cappers offer several advantages for smaller to medium-sized production scales. Their design often provides more precise control and handling of individual caps. This makes them suitable for operations where accuracy and attention to detail are paramount, such as in specialized or custom packaging.
They tend to be more flexible in terms of accommodating different cap sizes and types, allowing for quick adjustments and changes in the production process. This adaptability is beneficial for businesses with diverse product lines or frequent packaging modifications.
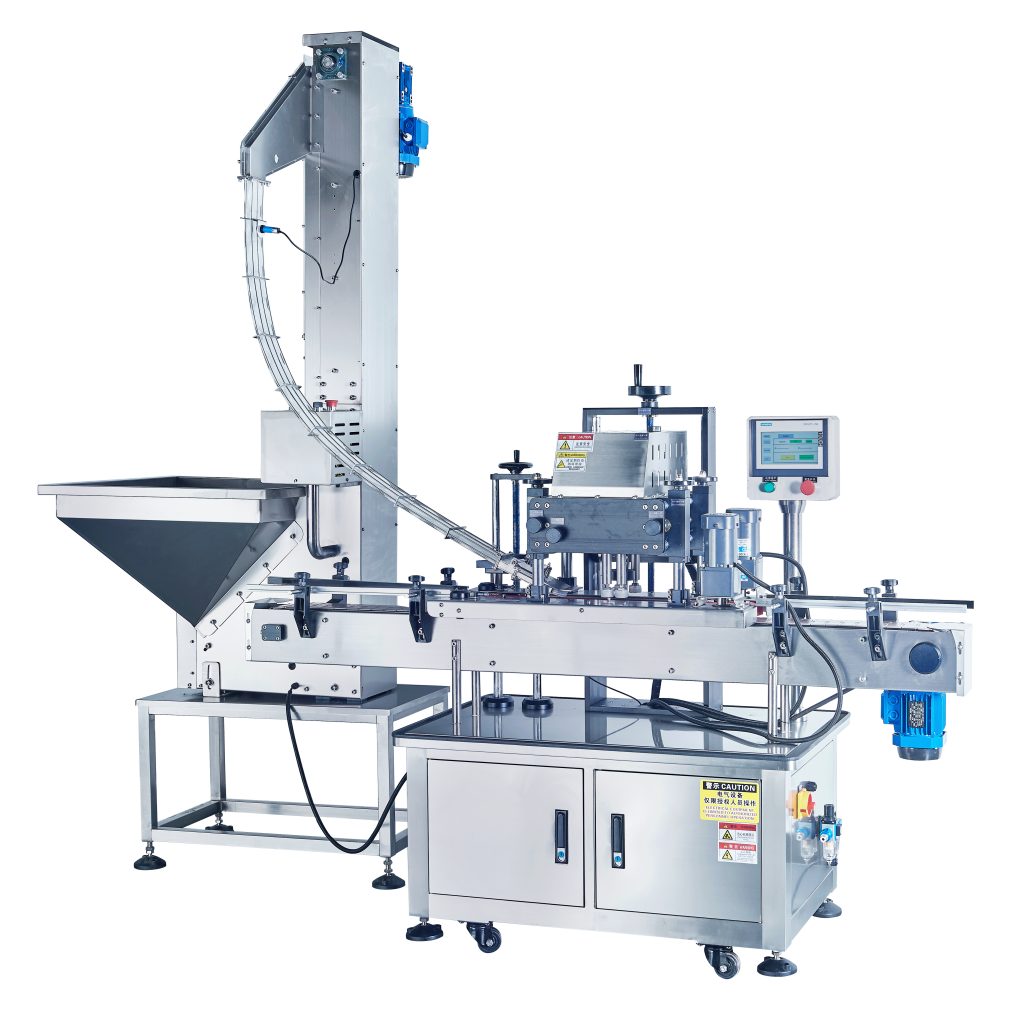
On the other hand, rotary cappers shine in large-scale production environments. Their continuous rotational motion enables a high-speed capping process, maximizing output and productivity. They are ideal for mass production runs where speed and volume are the primary concerns.
However, rotary cappers may require a larger initial investment and more complex maintenance. They might also be less flexible when it comes to rapid changes in cap specifications.
Ultimately, the choice between 4-wheel and rotary cappers depends on your specific production volume, product variety, budget, and operational requirements. Careful assessment of these factors will help you determine which type of capper is the best fit for your production scale and ensures a smooth and efficient packaging operation.