Semi-automatic can seamers play a significant role in enhancing packaging efficiency in several ways.
Firstly, they offer speed and consistency in the seaming process. Compared to manual methods, semi-automatic machines operate at a much faster pace, allowing for a higher volume of cans to be sealed in a shorter period of time. The consistent pressure and movement applied during seaming ensure that each can is sealed with uniform quality, reducing the likelihood of defects and rework.
These machines also minimize human error. Manual seaming can be prone to variations in pressure and alignment, but semi-automatic can seamers follow precise settings and procedures, resulting in more accurate and reliable seals. This not only improves the quality of the packaging but also saves time spent on correcting mistakes.
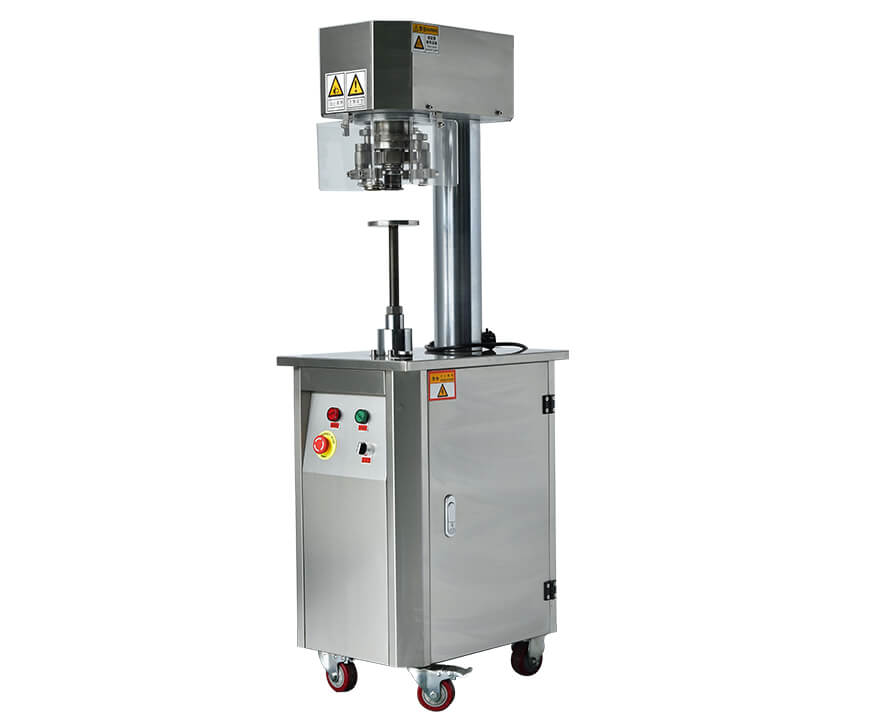
The simplicity of operation of semi-automatic can seamers enables operators to become proficient quickly. With less complex controls and processes, workers can focus on maximizing productivity rather than struggling with complicated machinery.
Furthermore, they contribute to better workflow organization. By integrating semi-automatic can seamers into the packaging line, the overall process becomes more streamlined, reducing bottlenecks and improving the coordination between different stages of packaging.
In addition, these machines often have features such as quick changeover capabilities for different can sizes or types. This flexibility allows for seamless transitions between production runs, minimizing downtime and maximizing the utilization of the equipment.
Overall, the combination of speed, accuracy, ease of use, and flexibility makes semi-automatic can seamers a valuable tool for significantly improving packaging efficiency.